Sheffield, United Kingdom | 2024 – The GMT® One System has been designed and developed by a large number of people and organisations that are collectively referred to as the GMT Consortium. The GMT® One System is comprised of thirty novel developments. It incorporates technology with international patents that are pending and a number of design registrations. The manufacturing intellectual property all resides within Wilson Benesch. As such it is inconceivable that another turntable with GMT® technologies will emerge. Two product names are trademarked GMT® and GRAVITON®.
Made in Sheffield
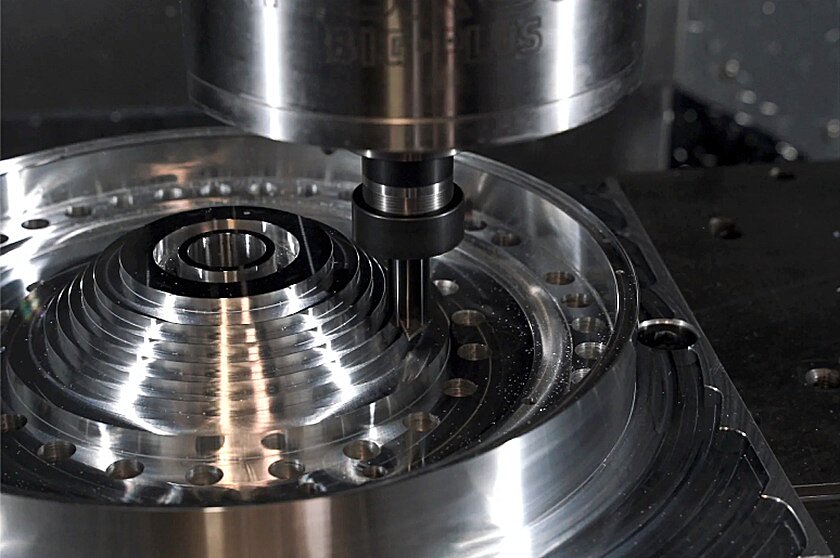
Wilson Benesch is a proud product of Sheffield, a city known globally for its rich industrial heritage and expertise in various fields of material science and engineering. In 2024 this rich heritage is evident through the presence of esteemed institutions like The University of Sheffield and The Sheffield Hallam University, but also in the Advanced Manufacturing Research Centre and the Advanced Manufacturing Park which now hosts major manufacturing and research centres for McLaren Automotive, Rolls-Royce and BAE Systems to name but a few. As a result of its heritage and continued presence as a centre for engineering excellence, Sheffield continues to attract a talented, highly trained engineering workforce and international students.
In 2024 Wilson Benesch operates from a 25,000 square foot facility. Within this facility the company has invested consistently through its 35-year history in cutting-edge manufacturing systems, operating a fleet of CNC Centres, along with all carbon fibre and bio-composite manufacturing systems. A twenty strong workforce is comprised of expert technicians and highly trained engineers. Wilson Benesch is and has been at the forefront of the high-end audio industry for more than three-decades, introducing cutting-edge technologies not limited only to the products themselves, but also to the materials that synthesise these products and also the manufacturing systems used to create them.
Wilson Benesch has consistently pioneered in material innovation within the audio industry. The brand has a track record of introducing novel materials ahead of its competitors. Whilst Carbon Fibre is synonymous with Wilson Benesch, the company has also been instrumental in advancing the use of RTM (Resin Transfer Moulding) technology since 1996, a technique that was relatively unknown at the time. The incorporation of Carbon-Nanotube and Graphene enhanced pre-preg in the various A.C.T. Tonearm’s that the company introduced from 1991 to the early 2000s showcased the company’s commitment to utilising cutting-edge materials long before they became mainstream in audio design.
More recently Wilson Benesch has made a significant breakthrough by introducing the world’s first bio-composite based loudspeaker enclosures.
This breakthrough new materials technology was possible thanks to Wilson Benesch’s participation by invitation to the SSUCHY Horizon 2020 Grant Project that had a €7.4-million budget. The result of this project marks a new era in audio design that set a new benchmark in the performance and application of composite structures, logically where Wilson Benesch led with Carbon Fibre in the audio industry and others followed, it is expected that others will now follow and adopt bio-based composite structures within future audio product designs in the coming years.
In addition, Wilson Benesch embraced additive “3D Printing” manufacturing technologies at an early stage, indeed some of the first components developed through the first grant project that Wilson Benesch undertook in 2008 entitled “The Mondrian Project” were entirely based on additively manufactured components. These components were manufactured at the AMRC in Sheffield, and it was ultimately work completed in collaboration with The University of Sheffield, Renishaw PLC and The AMRC that would lead to the final production models of all additively Selective Laser Sintered (SLS) manufactured Titanium parts in the Graviton® Armwand and the Tessellate Cartridges. Additive manufacturing has played a crucial role in the accelerated development of various subsystems of the GMT® One System as well as transforming the performance capabilities of the Graviton® tonearm.Wilson Benesch now operates a fleet of MarkForged additive manufacturing centres within its factory in Sheffield.
The above examples are just a glimpse of the vast intellectual property that forms the foundation of Wilson Benesch’s creative capabilities. The company’s success stems not only from its cutting-edge systems and manufacturing excellence but also from the exceptional craftsmanship of its highly skilled team. Many of these individuals have dedicated decades to bringing Wilson Benesch designs to life, showcasing their unwavering dedication, passion, and talent.
It is the collective efforts of these craftspeople that infuse Wilson Benesch products with an intangible quality rarely found in today’s manufacturing landscape. Their expertise and attention to detail result in products that are instantly recognisable even from a distance, serving as a testament to their collective artistry and commitment to excellence.
GMT® One System Turntable
GMT® One System is a collection of completely new solutions that have been brought together to create one harmonious analogue replay system. Every aspect of the design serves a purpose, leaving no room for redundancy or embellishment. Interdependent systems are harmonised and finely tuned through careful material choice and novel design that extract incremental and cumulative improvements that go beyond the sum of the parts.
Beyond technical considerations, the GMT® One System acknowledges the precious nature of its task. It is designed for those who value their vinyl record collections not just as possessions but as a responsibility, it is designed for the archivist. Similar to a fine watch, classic car, or cherished family heirloom, ownership is transient, and preservation is paramount. This understanding of the profound significance of music and its contribution to life is woven into every aspect of the GMT® One System.
To date almost all turntable designs rely on technologies that restrict any potential for significant improvement in performance. Examples of such technologies include belt drives, coil springs for isolation, screw threads for precision adjustment, and a tendency to increase the mass of a turntable to increase its perceived value.
Another almost ubiquitous element of other analogue systems is the assembly of multiple sub-systems, bringing together products from two or three different brands to assemble a system. The GMT® One System eliminates the potential pitfalls of an assembly of third party products by providing a unified interdependency between components so as to create one homogeneous whole. This is achieved through the utilisation of advanced materials science, cutting-edge manufacturing techniques, meticulous attention to geometrical precision and novel ways of approaching the problem. Some of the more notable developments have entirely eliminated the potential for inaccuracy and poor setup and installation.
The Unified System design approach that was first seen in the Wilson Benesch Total System of 1996 aims to bring harmony to system design that goes beyond the turntable and includes the phono stage as an integral and adjustable element also. The critical aim in this case is to preserve the precious millivolt signals of the MC cartridge, again, driven by the credo of building in cumulative improvements rather than cumulative errors. When sub-systems are optimised to seamlessly work together, the overall quality of the system surpasses the sum of its individual parts. Comprised of no fewer than 27 completely novel developments the GMT® One System’s unified design produces a new reference for analogue replay.
OMEGA Drive
Invented for one purpose only, the OMEGA Drive and ALPHA Drive designs were developed by a team of Doctors, Professors and Engineers formed under the GMT Consortium in 2019. This team was brought together with the aid of £326,000 of public funding from Innovate UK. The collaborative team comprised of Dr Faris Al Naemi, Dr Jon Travis and Professor Cockerham of The Sheffield University and Dr Carl Broomfield and Neil Broomfield of CAAS Audio. However, the pursuit of a turntable drive that meet the highest standards of audio quality and minimal deviations in the time domain has been a significant challenge extending over two-decades and this work can be found through publicly funded and therefore publicly available grant projects originally under the project name ‘The Mondrian Project’.
The OMEGA Drive motor is a collection of diverse technologies developed through expertise in electro-magnetic structural engineering, dynamic electro-magnetics, coil winding and precision machining of metals and polymers. The circumjacent radial force design of the OMEGA Drive motor provides a unique method of power transmission, resulting in smooth and precise rotation of the turntable platter. This innovative design eliminates the noise and vibration of all prior art. The OMEGA Drive is a slot less synchronous motor, delivering vanishingly low torque ripple and speed stability. The RMS value of the torque ripple is 0.001342 (N.m). The torque ripple includes all the components (like cogging torque and the current commutation and air-gap flux harmonics).
Prof. Eric Laithwaite of The UniversIty of Manchester who invented the linear motor derived an equation of “goodness” which described motor efficiency in general terms and in which he interpreted that motor efficiency increases with size and thus “goodness” increases as efficiency increases. At 15” the OMEGA Drive is the largest motor ever designed and developed for a turntable. The most commonly used direct drive motor in turntable design today is just 3.07”, five times smaller than the OMEGA Drive.
However, there are multiple complex factors that govern the performance of a motor. The position the coils, the density of the coil winding, the position of the magnets, the strength and flux pattern of the magnets, the mass of the moving components, the method of delivering the current to the system and of course the crucial design of the bearing.
During the development, WB evaluated and eventually defined the exact size of the rotor and the placement of the NDFeB magnets. This process was conducted using finite element modelling and evaluated skewing and complex NdFeB geometrical forms. WB also invested in coil winding machinery and recruited a graduate to work exclusively to work on this task. Precision mandrels were developed to interactively define the geometry of the coils.
The stator is responsible for governing the synchronicity of the rotor. It achieves unprecedented levels of accuracy with minimal torque ripple, no noise and zero cogging. Once synchronicity is achieved the system requires no feedback or complex speed compensation; the simplicity of a synchronous motor ensures exceptional speed stability.
Magnetic Counter Force Design
Accurately calculating Hertzian forces is crucial in engineering mechanical systems, especially in turntables and tonearms with single point contact designs. The analysis of Hertzian forces becomes vital due to the high pressure levels applied to materials. The OMEGA Drive motor, weighing 14kg (31lbs), is the largest motor designed for a turntable.
Following a comprehensive analysis conducted by The Sheffield Hallam University, led by Dr. Faris Al-Naemi, a magnetic counter force design was developed to reduce the overall mass of the dynamic parts that comprise the platter. This design incorporates two powerful N30H NdFeB magnets to ensure that the Hertzian forces at the contact point of the Angstrom bearing are well within tolerance limits. This approach minimises wear and provides sufficient force for the efficient transfer of energy from the platter to the entire system within the FrACTal Motor Chassis.
The combination of these features results in a turntable design that is unmatched in elegance, simplicity and precision. The body of work represents the largest study of direct drive motor design ever undertaken by any audio company and the results are a valuable IP asset protected by a patent.
The Unified System design approach that was first seen in the Wilson Benesch Total System of 1996 aims to bring harmony to system design that goes beyond the turntable and includes the phono stage as an integral and adjustable element also. The critical aim in this case is to preserve the precious millivolt signals of the MC cartridge, again, driven by the credo of building in cumulative improvements rather than cumulative errors. When sub-systems are optimised to seamlessly work together, the overall quality of the system surpasses the sum of its individual parts. Comprised of no fewer than 27 completely novel developments the GMT® One System’s unified design produces a new reference for analogue replay.
ALPHA Drive
The ALPHA Drive was developed in parallel with the OMEGA Drive motor. It is a sophisticated set of electronics that is design to deliver low torque to minimise torque ripple, which is a major challenge in motor drives. A novel start up algorithm is delivered by the onboard micro-processor which overcomes the significant air gap between the stator and the rotor in the OMEGA Drive. The OMEGA Drive then accelerates to synchronicity. Constant speed is then maintained by the micro-processor in the ALPHA Drive which delivers three pure sine waves via three linear class-A amplifiers to the 21 magnetic poles in the OMEGA Drive. The sine wave accuracy is governed by an onboard 11.2896 MHz quartz crystal. One phase is delivered to 7 poles in a 7by7by7 formation. Each phase has its own discrete linear class-A amplifier that delivers a low distortion 1.2amp high-quality sine wave.
The synchronisation of the motor and the high inertia of the platter are the driving forces behind the OMEGA Drive’s exceptional precision. There are Hall sensors which monitor the speed and ensure that the armwand Piezo VTA Control System cannot function until precise and accurate speed has been attained in the OMEGA Drive.
LeVeL Isolation System
Wilson Benesch’s development of the LeVeL Isolation System underscores the importance of structural stability in high-precision systems like the GMT® One System. By collaborating with Thorlabs, a renowned manufacturer of optomechanical isolation systems, Wilson Benesch ensures that the foundation for their system meets the highest standards of reliability and performance.
The LeVeL Isolation System operates at the microscopic level, addressing concerns about resonance that are crucial in both measurement and transcription applications, such as vinyl transcription. Utilising four micro-processor-controlled pneumatic rams, the LeVeL System continuously monitors and adjusts the GMT® One System with remarkable precision, ensuring stability even in the face of disturbances. The system’s resonant frequency of 1.7 Hertz further attests to its effectiveness in mitigating resonance issues.
Addressing concerns such as centre of gravity and equal distribution of mass at all four supporting points, the LeVeL System has been designed to perfectly offset the mass of the off-axis OMEGA Drive motor, Graviton® Armwand, Piezo VTA Control System and STAGE One that all reside upon it. WB have meticulously designed, and precision machined the LeVeL Isolation System plinth, such that it adheres to the inverted pyramid form that is critical for the Thorlabs system to operate optimally. With decades of use in demanding laboratory environments, the LeVeL Isolation System with the Thorlabs system at its heart provides a reliable platform for the GMT® One System to deliver ultimate reference accuracy and consistency.
In addition is also provides another barrier to spurious energy in the listening room from entering the most sensitive elements of the GMT® One System.
A medical grade air compressor system is provided with the LeVeL Isolation System. This is a discrete, oil-free compressor that only operates if a significant disturbance to the LeVeL Isolation System occurs. It can be installed in a separate room away from the GMT® One System.
STAGE One
The STAGE One’s innovative “over arm” design represents a significant advancement in the step-up process for cartridge micro voltages. By positioning the step-up stage directly above the tonearm, this design achieves an unprecedented level of proximity between the cartridge and the step-up stage. This closeness minimises signal losses and distortion, ensuring that the delicate signals from the cartridge are preserved with utmost fidelity.
One of the primary benefits of this design is the elimination of the need for multiple interconnects and long cables. By establishing a direct connection between the cartridge and the step-up stage, the STAGE One mitigates the potential for signal degradation that can occur with extended cable runs. Additionally, by minimising the distance travelled by the signal, the STAGE One reduces susceptibility to external environmental electromagnetic interference (EMF), further enhancing signal integrity.
The cartridge in a record player is the origin of all the sound that is heard, making its geometry and material design critical to the overall performance of the system.
Wilson Benesch developed its first cartridge systems in the early 1990s, in collaboration with Benz-Micro. Wilson Benesch designed and manufactured the world’s first carbon fibre cartridge body and the worl’d first carbon fibre headshell. Benz-Micro in turn mounted the generator to complete three cartridge options, the Ply, the Carbon and the Analogue cartridges. Much of the research completed in the development of these cartridges has informed the modern era of cartridge design now seen in the TESSELLATE Ti Cartridges.
Advanced Geometric Optimisation:
The TESSELLATE Ti Cartridges represent the pinnacle of geometric optimisation in cartridge structures. Developed in collaboration with Renishaw PLC and the University of Sheffield, the TESSELLATE Ti Cartridge body and headshell is manufactured using State-of-the-Art 3D additive manufacturing technology. Selective Laser Sintering (SLS) additive manufacturing technology uses multiple high-power lasers to weld together particles of titanium layer-by-layer to construct a single-piece cartridge body. There is zero redundancy of materials, resulting in a structure entirely devoid of unnecessary mass. The Wilson Benesch design team, in collaboration with Renishaw PLC, also optimised the structure to create a tessellated internal configuration that provides anisotropic material properties similar to those found in a crystal structure. This unique structure delivers levels of internal damping that have previously unattainable.
Semi-Open Architecture:
The semi-open architecture of the TESSELLATE Ti Cartridge headshell design is informed by the research completed in the development of the Ply, Carbon and Analogue cartridges. During this development, Wilson Benesch found that by changing the headshell geometry surrounding the cantilever, from a flat surface in the Analogue cartridge to a curved headshell surface in the Carbon cartridge, Wilson Benesch were able to achieve significant sonic benefits. The curved geometry increased stiffness and eliminated reflective surfaces, thus avoiding high Q resonances. The TESSELLATE Ti Cartridge adopts this semi-open structure, achieving maximum stiffness, minimum mass, maximum damping, and reducing reflective surfaces to a minimum. The design is highly evolved and optimised.
Hybrid Cantilever Design:
The TESSELLATE Ti Cartridge features an innovative hybrid cantilever design combining advanced cantilever systems with unidirectional (U.D.) carbon fibre damping. This results in enhanced tracking ability due to reduced resonance. U.D. carbon fibre adds virtually no additional mass but, when placed in the middle of the cantilever in an offset asymmetrical position, provides significant additional stiffness and damping.
The hybrid cantilever is available in various materials, including Boron, Sapphire, and Diamond. Each material offers unique characteristics that contribute to the overall performance and sound quality of the cartridge. Whether your priority is accuracy, transparency, or sonic refinement, there is a cartridge with a hybrid cantilever to suit your needs.
PIEZO VTA System
The ability to make VTA (Vertical Tracking Angle) or stylus rake angle adjustments from the listening position represents a significant advancement in turntable technology, offering a multitude of benefits previously unattainable. This capability is made possible by the precision of the Eco-Grip chuck, which facilitates precise adjustment without sacrificing accuracy.
The patented Eco-Grip chuck ensures that adjustments are made with exceptional precision. Unlike traditional screw thread methods, the use of a linear piezo actuator allows for adjustments with an incredible accuracy of 1 nanometer, which is repeatable. To put this into perspective, the diameter of a human hair falls within the range of 80,000 to 100,000 nanometers, highlighting the remarkable precision achieved by this system.
The Eco-Grip chuck exemplifies high precision engineering. Its design allows for the accurate definition of the bearing to tonearm dimension and facilitates adjustment of the VTA shaft of the GRAVITON® Armwand. The entire surface of the chuck conforms to the shaft surface, and the use of graphite lubricant ensures smooth movement without compromising accuracy. Additionally, the unique design of the chuck provides the option to clamp the VTA arm shaft in position without altering the arm’s geometry, further enhancing the precision and stability of adjustments.
Overall, the integration of the Eco-Grip chuck and digital control technologies represents a significant advancement in turntable design, offering unparalleled precision and control over critical adjustments such as VTA. This level of engineering excellence ensures that users can achieve optimal performance and playback quality with utmost accuracy and reliability.
WB GMT® Control APP
The integration of the WB GMT® Control APP into the GMT® One System represents a significant leap forward in user control and convenience. With this powerful graphical user interface, users have the ability to interact remotely with all aspects of the system, providing unprecedented control over key functions.
Wilson Benesch’s decision to supply a SMART Device preinstalled with the WB GMT® Control APP underscores their commitment to providing a seamless user experience. In addition, the GMT® One System ships with a router that is preconfigured to connect exclusively with the SMART Device and the GMT® One System ensuring effortless control of the GMT® One System.
Through the GMT® Control APP, users can finely tune various parameters to tailor their listening experience to their preferences. This includes adjusting the speed of the OMEGA Drive to accommodate different record formats, with the ability to fine-tune the speed in incredibly precise increments of 0.01 RPM. Users can also easily start and stop the OMEGA Drive, as well as lift and lower the GRAVITON® Ti Armwand with precision.
Furthermore, the GMT® Control APP enables users to adjust the PIZEO VTA System with remarkable precision, allowing for micro-level adjustments in 1 nanometer steps. This level of control over critical aspects of a turntable system is unprecedented and it legislates that users can achieve optimal performance and playback quality with unparalleled accuracy.
Overall, the integration of the WB GMT® Control APP into the GMT® One System sets a new standard for user control and precision in turntable systems. With its intuitive interface and comprehensive feature set, it empowers users to fully customise their listening experience with unprecedented levels of control and accuracy.
OMEGA Drive | Description | Synchronous 15” diameter, 21 coreless-slotless, 3 phase zero-cogging, zero torque ripple, patent applied for direct drive motor. The time-average torque is 0.718 N.m @ 1.2A RMS & rated speed of 33.3 rpm. The RMS value of the torque ripple is 0.001342 (N.m). The torque ripple includes all the components (like cogging torque and the current commutation and air-gap flux harmonics). | ||
ALPHA Drive | Computer controlled quartz referenced high precision sine waves. 3 super linear class A amplifiers. Computer controlled remote control systems. Computer controlled pneumatic self-levelling control for LeVeL isolation system. | |||
Speed Range | 33.3, 45, and 78pm | |||
Control | fully adjustable via dedicated Smart Device WB Control APP in 0.01 increments. | |||
Wow and Flutter | not measurable | |||
GRAVITON Ti Armwand | Description | Kinematic bearing provides 3-point location ensuring zero Brinelling and the optimal hertzian forces to ensure energy transfer through two different materials. Bearing is designed to allow easy change of Graviton® Armwand in less than a minute. Shortest possible lead out wire to avoid signal corruption. | ||
Internal Wiring | Silver / Teflon wire | |||
Effective Length | 304.8mm | |||
Mounting distance | 291.6mm | |||
Offset Angle | 18° | |||
Overhang | 13.2mm | |||
Effective Tonearm Mass | 14g | |||
Cartridge Weight Range | All possible | |||
TESSELLATE Ti Cartridge | Description | .D. Carbon fibre Hybrid cantilever Titanium body Micro ridge stylus cartridge system. | ||
Cantilever Options | Boron, Sapphire and Diamond available | |||
LeVeL Isolation System | Description | fully configurable according to specific requirements of any environment. No requirement for adjustment. Fully autonomous. |
||
STAGE One | Description | Stage One: Close proximity MC to MM step up transformer output and direct output option. | ||
R1 Rack | Description | Provides optimal location of all Alpha Drive & Omega Drive systems. Enables complete concealment of all energy systems. | ||
WB GMT Control APP | Description | Provide GUI for complete remote control over all critical aspects of system including VTA (accurate to 1nM) start / stop, speed and lift lower. | ||
Router & LAN | Router provided with the unit, preconfigured with wifi connection to the Smart Device preinstalled with the WB Control APP. Does not connect to the internet. | |||
Compressor | Medical grade silent running system to deliver energy to LeVeL pneumatic isolation system. | |||
Total System Weight | 369.5Kg // 523lbs |